The official website of Shanghai Songjiang Shock Absorber Group Co., Ltd. introduces you: high-speed wire finishing mill thin oil lubrication station rubber joint information, Songjiang Group provides high-quality rubber joints for many high-speed wire finishing mill thin oil lubrication stations, with a 3-year warranty.
With the continuous improvement of the rolling speed of rolling mills, higher requirements are put forward for the lubrication system, and with the development of science and technology, new technologies and new methods are constantly being applied to the control of the thin oil lubrication system.
High-speed wire refers to wire steel rolled by a high-speed rolling mill. The wire is divided into two types: rebar and coil. Some of the coils are divided into high-speed wire (high wire) and ordinary wire (normal wire) according to different rolling mills.
The high-speed wire is rolled on a high-speed wire rod mill. The production pace is fast, the coil is large (the coil in the package is usually a whole coil, and the maximum coil weight can reach 2500kg), and the packaging is usually tight and beautiful.
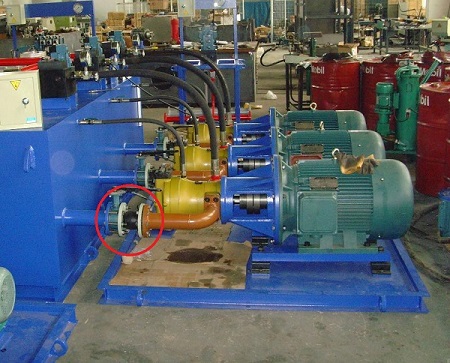
High-speed wire refers to wire rod rolled with a “high-speed non-twist rolling mill”. The rolling speed is 80-160 m/s, the weight (disk) is 1.8-2.5 tons, and the dimensional tolerance is high (up to 0.02mm). During the rolling process, the process parameters can be adjusted (especially in the cooling line). Above) to ensure the different requirements of the product.
Normal wire refers to the wire rod rolled by “ordinary rolling mill (generally horizontal double double rolling mill)”. The rolling speed is 20-60 m/s, and the weight (plate) is 0.4-0.6 tons per piece (the one seen in the market is generally three pieces and six heads as a large plate). During the rolling process, it can only be cooled by air on the cooling line. Or air cooling to ensure product performance. The general line is rolled by an ordinary rolling mill, and the weight of the coil is generally small. A package is usually packaged by several coils, and the package is loose and messy.
Finishing mills are used in high-speed wire rod workshops and generally consist of 4 rolling mills, all of which are cantilevered roll ring stands, arranged alternately horizontally and vertically. There are vertical loops between the stands to realize tension-free rolling.
The finishing mill is arranged behind the middle roller table or the coil-box of the rough rolling mill. Its equipment includes the front roller table of the cutting head flying shear, the side guide plate of the cutting head flying shear, the cutting head flying shear speed measuring device, the edge heater, the cutting head flying shear and the cutting head collecting device, the finishing rolling descaling box, and the finishing rolling mill. Front vertical rolling mill (FIE), finishing mill, looper device, finishing mill inlet and outlet guide plate, finishing mill dust removal device, finishing mill roll change device, etc.
Finishing rolling mill is a finished rolling mill and the core part of hot-rolled strip production. The quality level of rolled products mainly depends on the technical equipment level and control level of the finishing rolling mill. Therefore, in order to obtain high-quality and excellent products, a large number of new equipment, new technologies, new processes and high-precision detection instruments have been used in the finishing mill, such as hot-rolled strip shape control equipment, full hydraulic reduction devices, and most Jiahua shearing device, hot rolling oil lubrication process, etc. In addition, in order to protect the equipment and operating environment from pollution, a dust removal device is installed in the finishing mill.
After the slab is rolled by the rough rolling mill, the thickness of the intermediate billet is generally less than 50mm, and the thickness of special products is also up to 60mm. Due to the free state of the head and tail ends, the head and tail parts of the intermediate billet have different degrees of irregular fish tails or tongue shapes. Irregular head and tail shapes are prone to steel accidents when passing through the finishing mill or into the coiling machine. At the same time, due to the low temperature of the head and tail, it is easy to cause roll marks on the surface of the roll and affect the surface of the strip. quality. In order to prevent the occurrence of the above problems, the head and tail of the strip should be cut to a length of 100-150 ram with a cutting head flying shear. The sheared strip passes through a finishing rolling descaling box, and the oxide scale on the surface of the strip is removed with high-pressure water of 15.0-17.0MPa, and then enters the finishing mill to be rolled to the required strip size.
For some special products, such as silicon steel, stainless steel, cold-rolled deep-drawing steel, etc., before the intermediate billet enters the finishing mill, the edge of the strip is generally heated to make the temperature of the middle and edge of the strip uniform on the cross section. In this way, a strip steel with completely consistent metallographic structure and performance is obtained, and at the same time, edge cracks caused by low edge temperature and serious uneven and dense damage of the edge to the roll are avoided.
The thin oil station is the heart of the thin oil circulating lubrication system, which is used to force the lubricating oil to the friction part of the machine. Thin oil station is mainly used in the centralized lubrication system of dynamic and static pressure or sliding shoe bearings of metallurgy, mining, cement and other mechanical equipment, and is usually installed in underground oil depots or pits near the machine.
Thin oil station is an important guarantee for the normal operation of operating equipment such as blowers. If a serious leakage occurs during operation, it will cause serious losses to the executive components, and even cause major shutdowns. Even a slight leakage will adversely affect the on-site environment and safety production. The traditional method requires disassembly and maintenance, which is not only labor-intensive, but also causes a long-term shutdown, which seriously affects the continuous production of the enterprise. Polymer composite materials can be used for rapid on-site treatment, which shows fast, convenient, and durable characteristics when repairing such problems. It can eliminate the need for disassembly and on-site treatment of leaks without stopping or with less downtime.
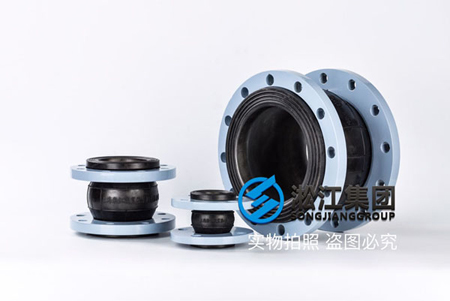